In response to the squeeze on resources, the world is moving from a 'take-make-dispose' model of consumption to a more circular approach, in which as little as possible is wasted and as much as possible reused. Steel's recyclability gives it an inherent advantage here, but there are commercial and technical challenges to overcome if we are to lead in this area.
Why is this important to us?
Every aspect of the way resources are used is now under question. From manufacture to product design to how goods and services are 'owned'. Global experts predict a new type of economy in which everything is either recycled or reused, and no raw materials or energy resources are wasted.
So, when we talk about efficiency, we mean it in the widest sense. We have a social, environmental and commercial responsibility to use resources efficiently, reducing our impacts and our raw material costs. In today's world, the industry is expected to reduce landfills to zero. We aim to ensure that the resources we use are put to the best possible use, taking advantage of steel-making processes to generate or reuse as many by-products as we can.
Our challenge
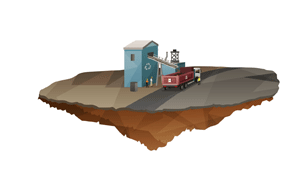
While steel is infinitely recyclable and is recycled at a global average rate of 87%, our challenge is to increase the supply of scrap. Today, global steel demand is three times higher than what global scrap supplies can meet. Research tells us that it is not until the latter part of the century will global scrap availability enable the majority of new steel to be made from old. Until then, iron ore will continue to be the main raw material used in steel production.
Another challenge is that steel scrap contains impurities, mainly copper. It means that scrap is better suited for making construction steel, which can accommodate these impurities, and less suited to higher grades of steel used in the automotive and home appliance sectors. So, that is not a problem yet. But when steel demand equals scrap supply, we will have to resolve this issue.
The next challenge is to use our by-products – slag, sludge, dust, process gases, heat and steam. For each tonne of steel we make, we also produce 0.6 tonnes of residues. We find markets for many of these by-products, and recycle our process gases too, but we have not yet found a use for all of them and we need to work harder on that.
Our action
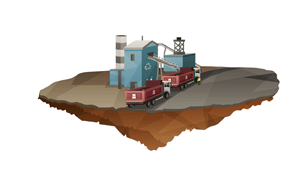
We need to continue to develop our production processes for more efficient resource use. In terms of scrap, this means working more with stakeholders to drive up recycling rates around the world until no steel ever goes to landfill. It also means working with the steel industry to develop cost-effective ways to clean scrap supplies from contamination.
In relation to our residues, we will make our processes even more efficient and reduce the amount of residues we produce. We need to increase our internal recycling rate and, where we cannot use the residues ourselves, use the residues ourselves we need to further develop markets to use our by-products. There is much to be done to have zero landfill waste.
Our potential to create value
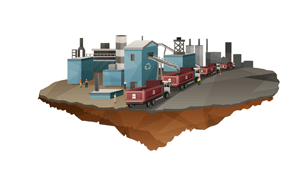
Steel plants are also recycling facilities, because scrap steel is an important input in the steel-making process. This makes us one of the world’s largest recyclers. Our track record in reusing our by-product, along with other industries and organizations, has made us a valuable partner. We see opportunities in business models emerging from our innovation programmes, which are inspired by more circular economy thinking. Rather than simply selling our slag to the cement industry, for example, we now have a joint venture with Ecocem and produce a cement substitute at two of our steel plants. We have industrial pilots to transform our waste gases into products for other industries – creating potential new revenue streams.
We are considering the potential of using waste from other industries in our steel-making. We are developing innovations that could have strong positive effects on how we create value.